Laminated Glass Keeps Tigers Out Of Your Bedroom (and Other Surprising Benefits of Using Laminated Glass in Architecture)
Given the number of conversations we have on the subject, perhaps laminated glass isn’t always appreciated for its full range of benefits.
We are seeing glass used more and more as a significant component of the architectural design of exterior envelopes. The trend doesn’t appear to be changing any time soon.
Expectations that glass should do more (and different) things has grown. And of course, architects have been bombarded with glass performance data ranging from actual breakthrough technologies to mere overblown hyperbole.
While we work on specifications for high-tech glass on a daily basis (switch-lite glass, bullet-proof and blast-proof glass, low iron, low reflectivity, STC ratings, etc.), we want to circle around to a product that’s been around a while: laminated glass. Given the number of conversations we have on the subject, perhaps laminated glass isn’t always appreciated for its full range of benefits.
A summary of the benefits can help in more clearly translating the value and applications where lami glass makes sense as an architectural specification.
Laminated glass is more potent than a moonshine milkshake on a Monday morning. It delivers a host of upside.
Laminated glass – the unsung superhero of glass world
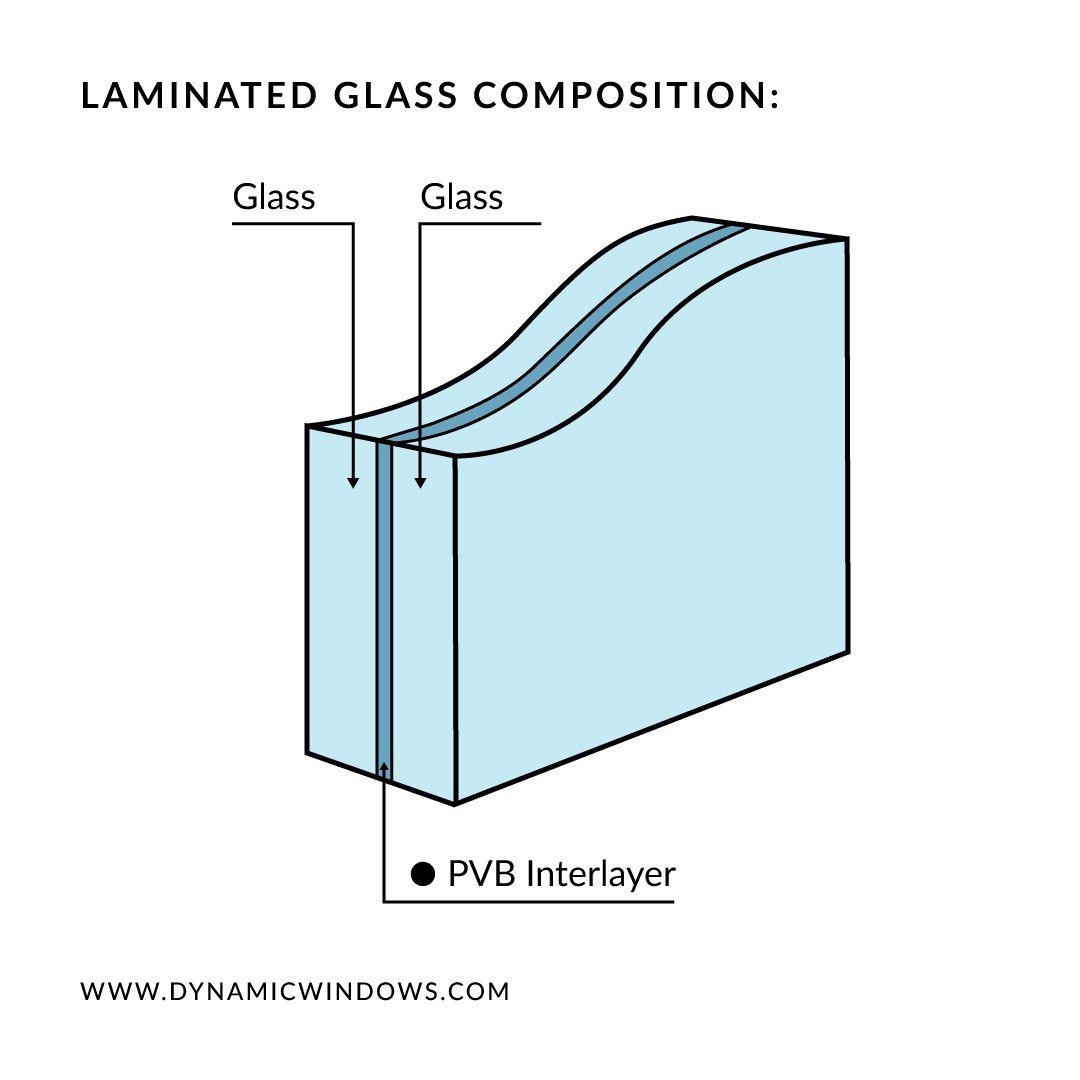
Laminated glass is made by taking two or more sheets of glass and sandwiching a polyvinyl butyl (PVB) membrane between them.
Laminated glass is multi-purpose and comes in many forms. It is so heroic it wears its underwear outside its pants like Superman. You’ve gotta be pretty impressive to pull that look off.
How Laminated Glass is Made
Laminated glass is made by taking two or more sheets of glass and sandwiching a polyvinyl butyl (PVB) membrane between them. The PVB membranes are available in a variety of thicknesses. Typically ranging from 0.15 (thinnest) to 0.90 (the gauge used for Hurricane Impact glass).
PVB membranes are typically clear and do not affect the Visual Light Transmittance (VLT) of the glazed opening. Solid color membranes are also available to create a glazed spandrel panel.
Key benefits of laminated glass:
Enhanced UV filtration
- Lami glass filters about 99% of the most damaging portion of the UV spectrum.
- UV filtration helps mitigate fading of interior finishes – art work, book collections, carpets, wood floors, drapes, furnishings etc. Mitigate is the key word here people – some degree of fading will still occur as there will still be daylight coming through.
- With modern windows taking up a much larger percentages of glazing in the envelope of the home, mitigating UV becomes a more prominent management issue. Laminated glass is a go-to solution.
- For owners who want to eliminate fading altogether you can offer to brick up all the openings or design a subterranean dwelling in northern Norway.
Enhanced sound abatement & Sound Transmission Class (STC) ratings
- Introducing a PVB membrane into the glass make up significantly enhances sound abatement properties by blocking sound waves and reducing vibration – particularly appealing in noisy urban applications.
- Different sounds travel on different wave lengths (frequencies). Different glazing thicknesses and membrane combinations can be utilized to address the more prominent noise issue – traffic or airplanes for example.
- For more extreme sound levels, laminated glass can be used on the inner and outer panes to increase the sound attenuation. Using a mixture of 3mm, 4mm, 5mm and 6mm glass thicknesses within the glass make-up is more effective than using a single glass thickness.
- There are specific interlayers being marketed as acoustic membranes – Trosifol is one example.
- The airspace(s) within the sealed units is an important contributor to sound attenuation.
- The fit of the sash to the frame as well as the design and effectiveness of the weather-stripping directly affect the sound blocking capabilities of the unit.
For more on Sound transmission Class (STC) ratings for windows, you can check out our STC Blog here.
Enhanced security with more robust PVB interlayers
Security and peace of mind are distinct benefits and both can be enhanced using laminated glass. With an appropriate PVB interlayer thickness, laminated glass can resist repeated hammer blows for an extended length of time without the glass actually coming out of the window. This buys time for the home security system to alert the authorities. Preventing entry rather than apprehending an intruder inside the home.
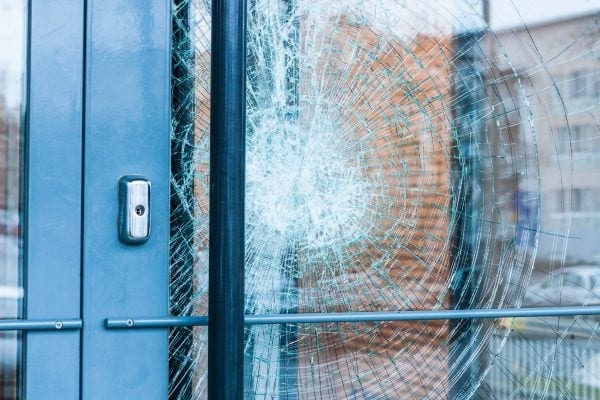
Laminated glass offers the security without the home looking like it has been fortified for a siege.
Resistance to forced entry is important to most homes and businesses. Especially those whose entrances are readily accessible from the street. But also more remote summer or winter getaway properties that may only be occupied for a few weeks in the year.
PVB interlayers come in different thicknesses as we mentioned. The thicker the interlayer, the more resilient it is under impact. Typically, a .090 thickness interlayer is the thickest interlayer that is commonly available.
Typically, PVB interlayers are clear and visually you can’t see they are included in the glass. So the security benefit is gained. All without any hint of the home looking like it has been fortified for a siege.
Safety from flying glass and debris
It’s easy to overlook a really basic fact – glass that shatters into shards, especially if the impact is hard enough to turn the shards into airborne projectiles, is a significant cause of injury.
Hurricanes or high winds are an obvious example but a person walking into a glass door is more common than many people think. We’ve all heard stories of Uncle Joe at the family barbeque on his third pint of Guinness walking slap dab into the living room glass sliding door, right?
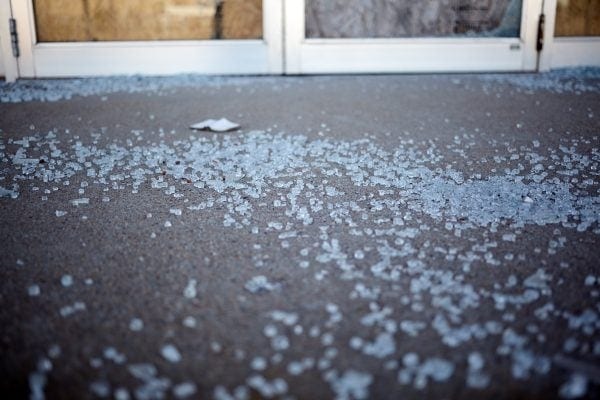
Laminated glass holds the shards together when broken under impact. Unlike tempered glass which breaks into thousands of small pieces.
The PVB membrane prevents glass shattering under impact – much like a windshield in a car. It holds all the shards together on the membrane so they cannot become lethal. By comparison, tempered glass when impacted breaks into thousands of small pieces that fall from the door or window.
Modern tempered glass is designed to disintegrate into relatively harmless granular pieces, which reduces some of the concern. Annealed (non-tempered) glass however, will break into sharp shards. This can be avoided with some forethought.
It’s worth looking at any windows and doors that would otherwise have annealed glass and considering laminated glass for those locations.
Hurricane impact glazing
Just because a piece of glass is laminated doesn’t make it Hurricane Impact glass.
Hurricane impact glazing codes have been, and still are, primarily driven by the insurance industry as they have a vested interest in minimizing damage to persons and property. They recognized some time ago that the right glazing plays a significant role in achieving this.
Hurricane Impact glass is laminated – always – but requites specific membranes that are robust enough to stop airborne debris.
Hurricane Impact glass is laminated – always – but requites specific membranes that are robust enough to stop airborne debris.
Many people have seen the tests where a 2 x 4 is placed in a cannon and fired into the center of the glass. The glass will break but not release from the frame – the interlayer holds the glass pieces together. With the glass staying in the frame, you avoid the sudden devastating change in air pressure which would lead to the roof being torn off.
The walls potentially collapsing and large chunks of the property turning up unexpectedly 200 miles away in rural Idaho. No wonder the insurance folks think it’s worth pushing for the right glass.
Hurricane impact glass – as a side note – requires a different glazing technique as well as the correct code compliant interlayer. After all, the glass has to stay in the frame. After passing third party testing and certification, the glass and frame only then are actually impact rated.
Reduce inherent visual distortion
There are multiple reasons why insulated glass units (IGUs) inherently have some level of visual glass distortion — wind loads, elevation, temperature, the way light travels through two panes of glass and so on. An insulating glass unit is a flexible pressure chamber in effect, when you get right down to it.
Where lami glass can help is in the area of limiting the distortion inherent in the heat treatment of tempered glass.
Lami glass can help by limiting the distortion inherent in the heat treatment of tempered glass.
Glass is heat treated to increase its strength to meet the various building specification requirements. All heat-strengthened and tempered glasses processed through horizontal roller hearth furnaces contain repeating lines or “waves” of glass thickness variation. Which extend across the width of the glass sheet as it passes through the oven.
The ceramic rollers that move the glass through the furnace produce very slight indentations into the glass surface at the temperature required for tempering.
If you walk down your local high street, you’ve probably noticed how your reflection in the storefront windows isn’t exactly pristine. Sometimes it can be look more like the mirrors in the Fun House at the local fairground.
Vertical furnace technology may eventually make roller distortion a thing of the past — but, while acknowledging the huge strides by the glass industry in this regard, we’re not quite there yet and glass isn’t perfect.
For more on glass quality standards, see our ASTM blog.
Laminated glass can be made with annealed (non-tempered) glass and providing annealed laminated glass meets wind load deflection criteria etc., it can replace tempered glass in many code requirement applications. Exterior glass doors are one example. With each pane of tempered glass eliminated, a level of visual distortion is avoided.
Non-tempered glass is not as strong as tempered, so review the potential switch in terms of wind load deflection. Your window fabricator should be able to offer assistance with this review.
It’s All Upside
To circle back to our comment that laminated glass may not always be appreciated for its full range of benefits, the upside is that an architect may specify lami glass for one of the principle benefits mentioned in this conversation. You may choose it for one specific reason — but you get all the other benefits by coming along for the ride.